On-site GNSS testing
Field testing, in real conditions, of terminals based on GNSS technologies
What are gnss field tests?
Tests in real situations aboard a light vehicle are usually the first carried out by users. They are often limited to position measurements around the premises with a very approximate idea of the trajectory actually traced by the on-board antenna.
Paradoxically, real tests are the most complex to analyze. On a test bench, the test conditions are known if not controlled. In the real world, multiple factors are likely to impact the measures. Where possible, on-site testing is reserved for the final integration phases.
WHERE SHOULD ON-SITE GNSS TESTS BE PERFORMED?
GUIDE has a well-equipped test vehicle to carry out data collection campaigns in previously characterized environments. However, this instrumentation has also been installed in different types of vehicles such as trains, trams, agricultural robots, boats, planes and helicopters.
Position measurements are carried out under the conditions most representative of the mission profiles.
Test campaigns can be planned to address the most specific of the client’s issues by benefiting from the client’s facilities.
The analyses take into account all the elements involved in determining positions.
Summary:
- Test configurations as close as possible to the mission profiles: environments, vehicles, dynamics and ambiant conditions;
- Benefits of the testing facilities made available to clients;
- Use, if necessary, of a fully equipped test vehicle.
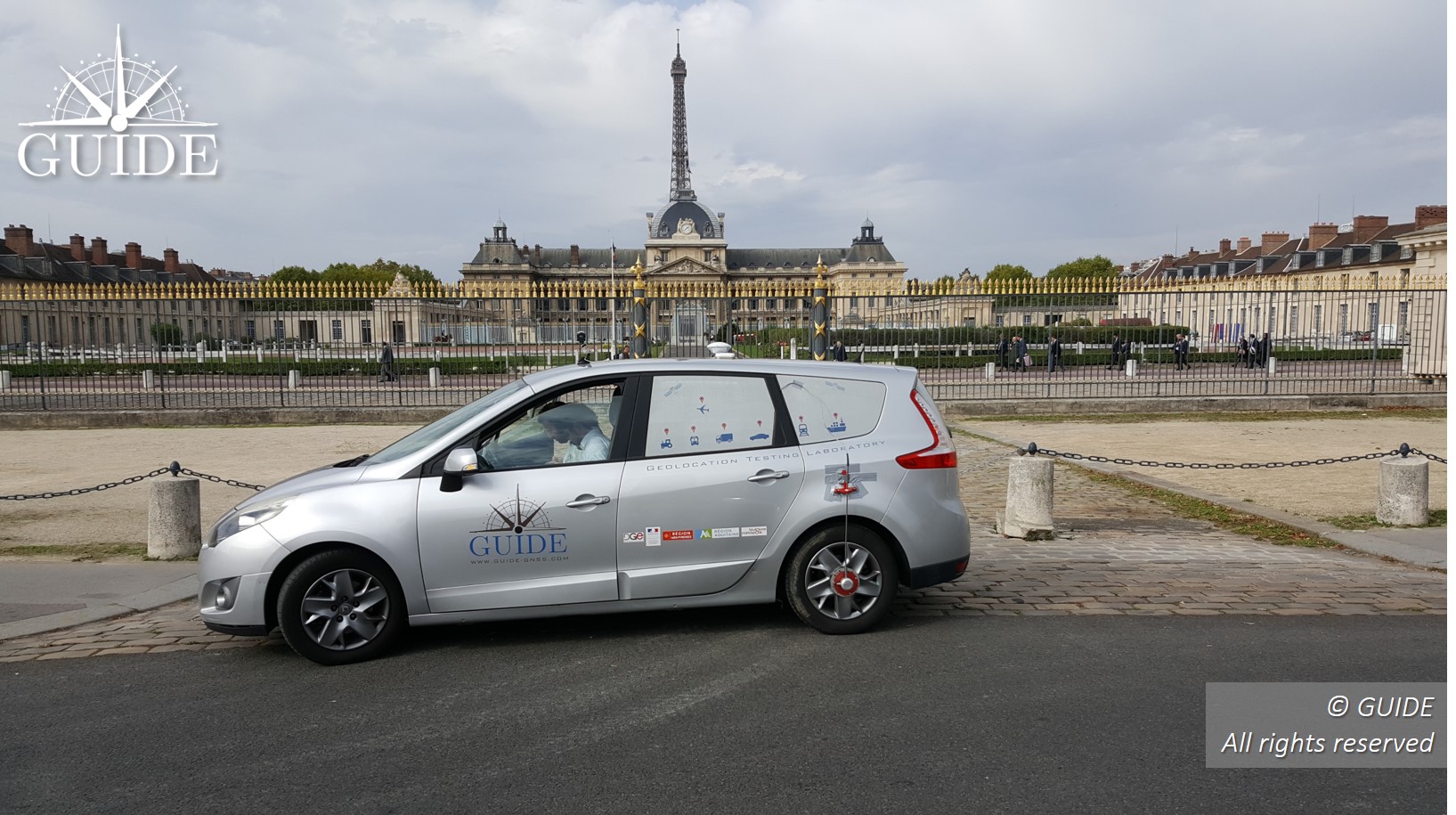
Why do on-site gnss tests?
The main advantage of data collection campaigns in real situations is to provide measurements representative of the missions to be completed. If by nature the test phases cannot be repeated, it is nevertheless possible to take on board instrumentation to digitize GNSS signals and to record sensor measurements for subsequent replay in the laboratory. This data will help improve the analyses.
Field tests are currently the only solution for evaluating positioning systems that use hybridizations of several technologies, such as GNSS receivers, NRTK corrections, Inertial Units, Odometers, etc. In addition, this type of test also integrates the installation and ambient conditions, such as vibrations, extreme temperatures or even electromagnetic waves susceptible to interfere with GNSS signals.
Besides implementing its metrology instrumentation, the GUIDE test laboratory brings its experience to identify the various factors to be considered in the analyses. The relevance of the recommendations will be directly conditioned by the choice of planned test cases.
Summary :
- Representative position measurements (and repetitive when digitizing and recording test data)
- Implementation of positioning systems integrating (hybridizing) all the equipment useful for geolocation
- Dependence on all the factors likely to influence the position measurements
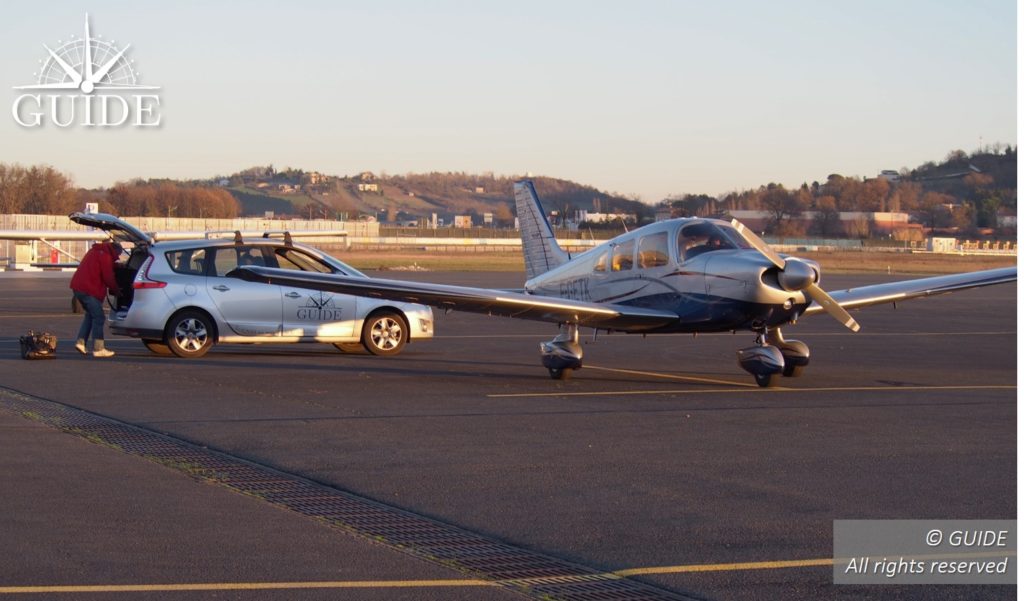
Figure 1 : GNSS test on board of an aircraft
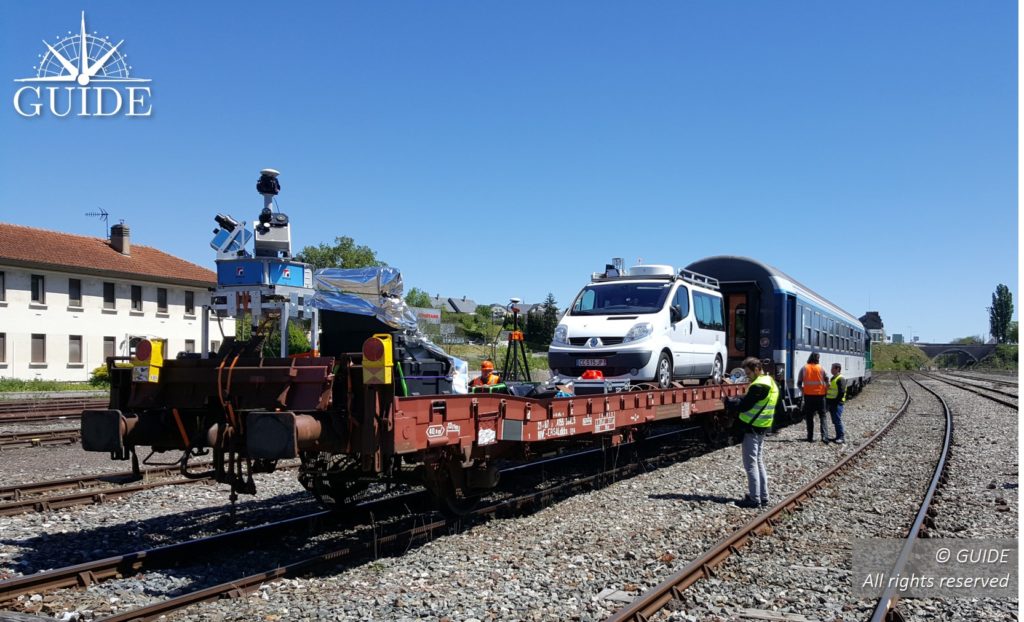
Figure 2 : GNSS test on board of a train
How to perform on-site gnss tests?
Planning for on-site testing begins with the identification of the areas that will be covered by the test vehicle. These must include the different types of environment likely to cause errors. A characterization of the selected environments is recommended in order to correctly link the different segments.
The equipped vehicle must be representative of those on which the GNSS terminals will be installed. If necessary, GUIDE can supply a pre-equipped minivan for a rapid implementation of measurement campaigns.
The test vehicle must embark the devices under test (DUT*) and metrology instrumentation including in particular:
- Reference instrumentation: an antenna, a professional GNSS receiver, a precision inertial unit and an odometer
- Digitization instrumentation
- Control instrumentation: metrology receiver, panoramic video
The position measurements recorded on the DUT will be compared with the consolidated ground truth from data provided by the reference instrumentation. Position errors are analysed in order to have the best possible DUT profile.
The use of a digitizer is often crucial to refine the analyses, in particular by isolating so-called “random” errors.
(*) DUT = Device Under Test.
Summary :
-
-
- Use of a given test vehicle with the provisions of the DUT
- Selection and characterization of test environments
- Vehicle instrumentation will provide a reference, digitization and control equipment
- Analysis of errors in position measurements.
-
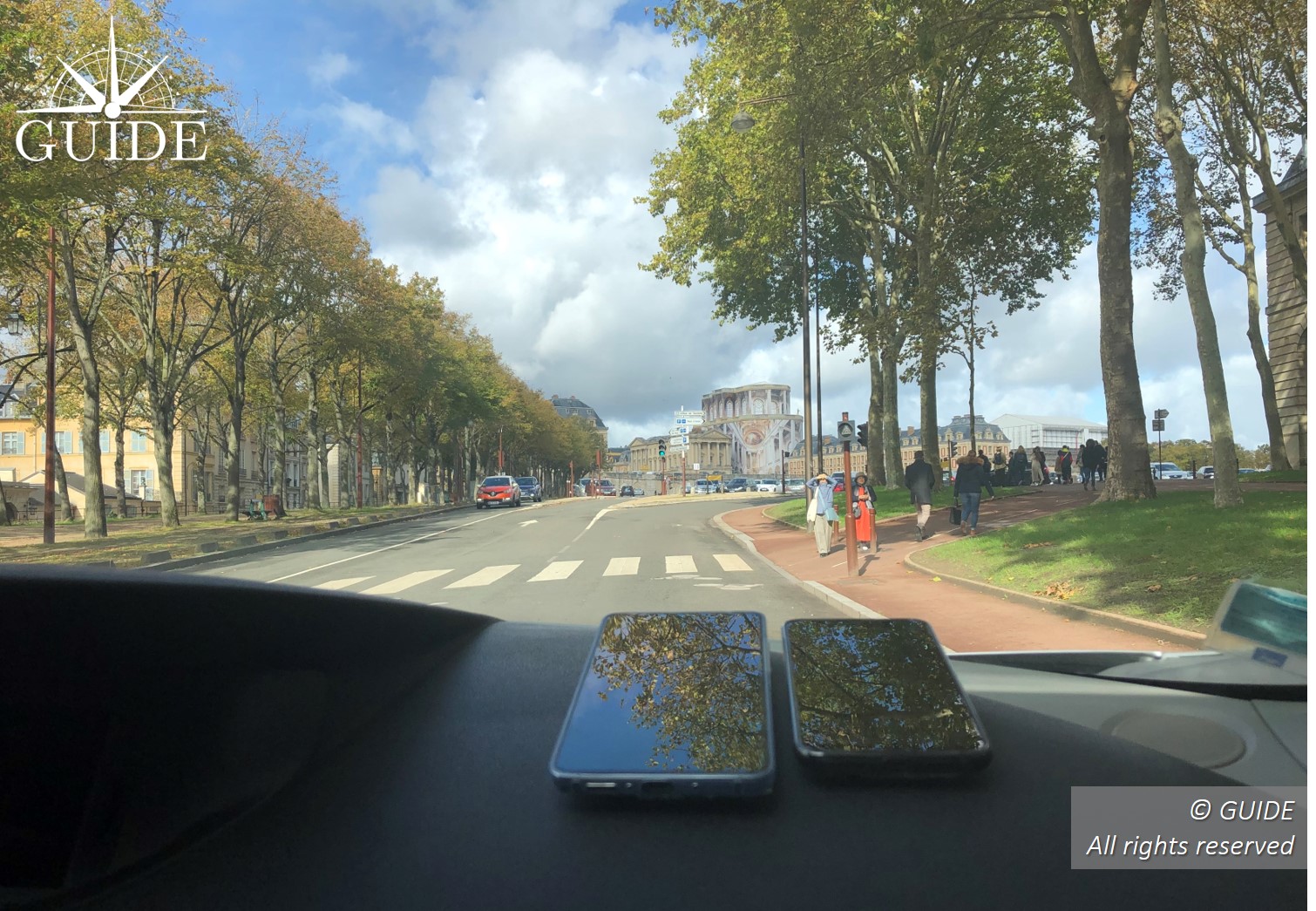
Figure 3 : GNSS test on board of a car
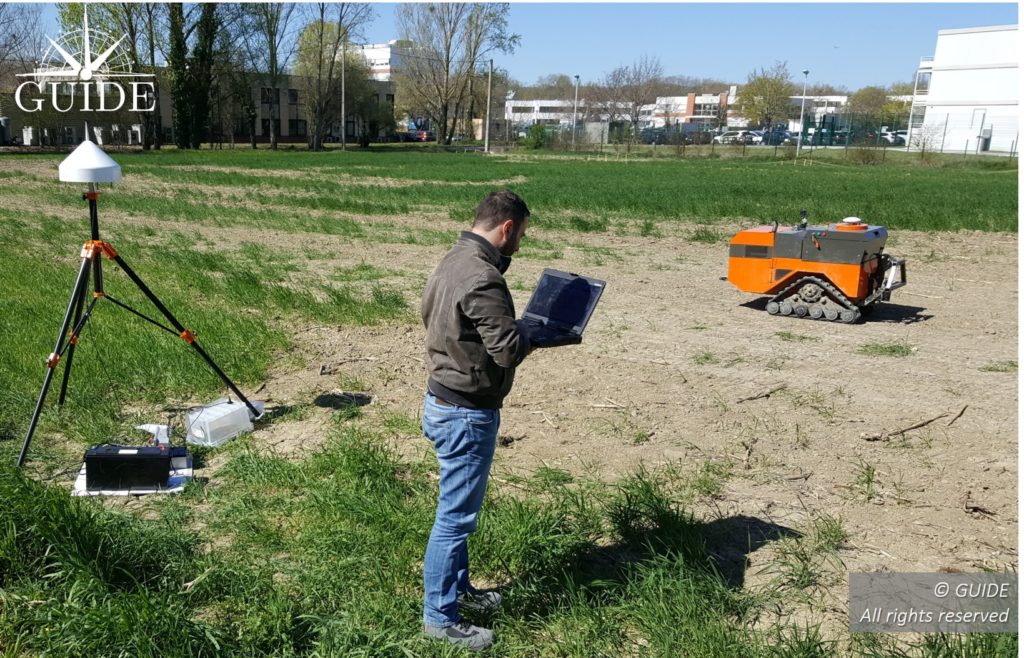
Figure 4 : GNSS test on board an agricultural robot with Agreenculture
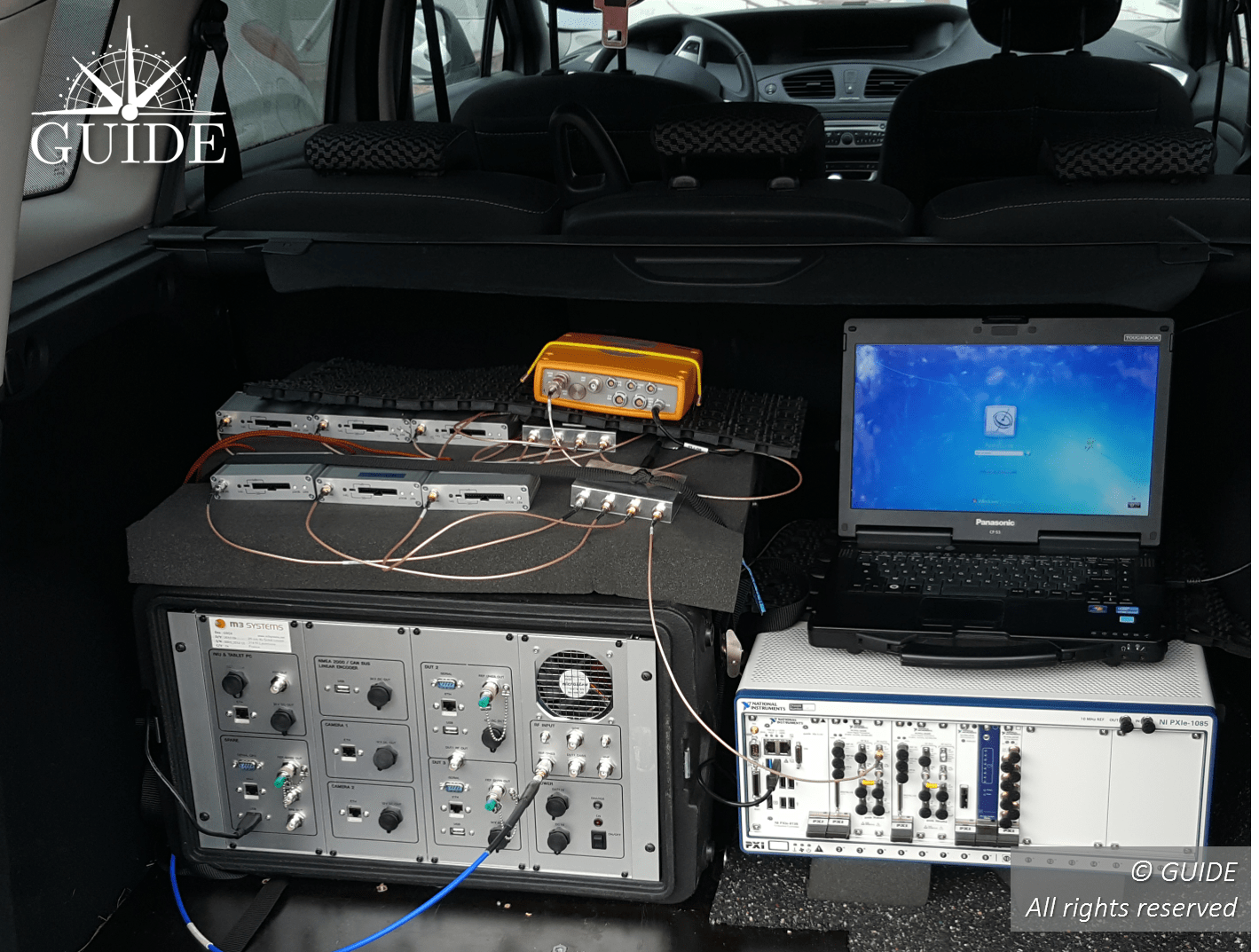
Figure 5 : GNSS instrumentation on board a test vehicle
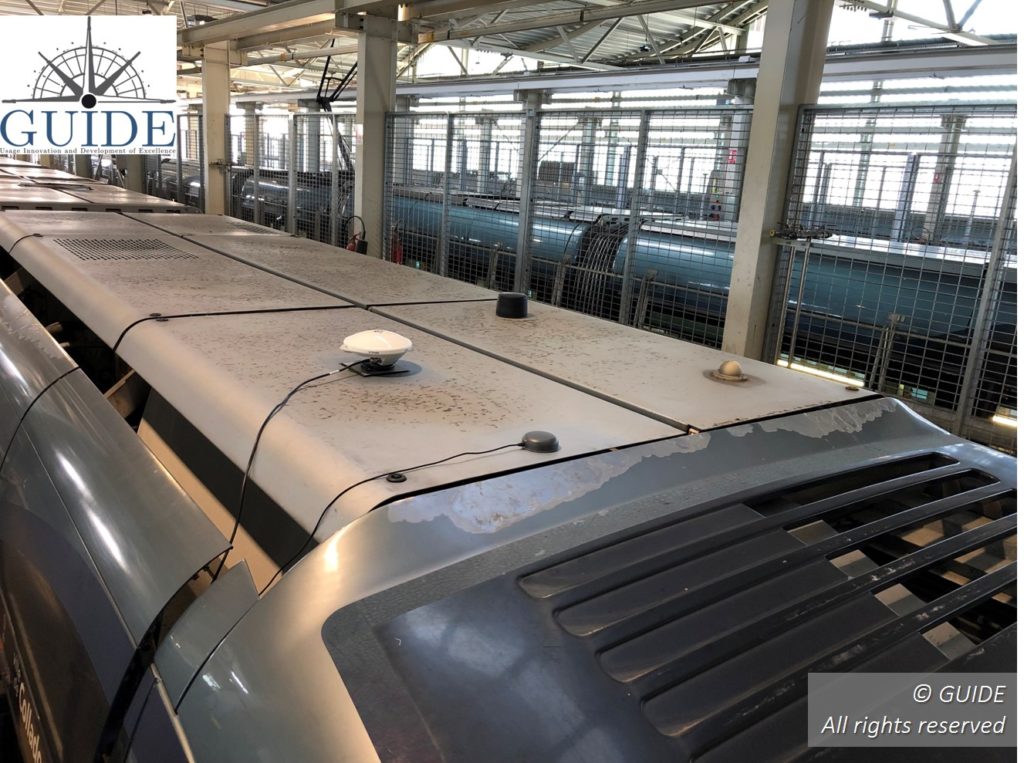
Figure 6 : GNSS test on board a tramway